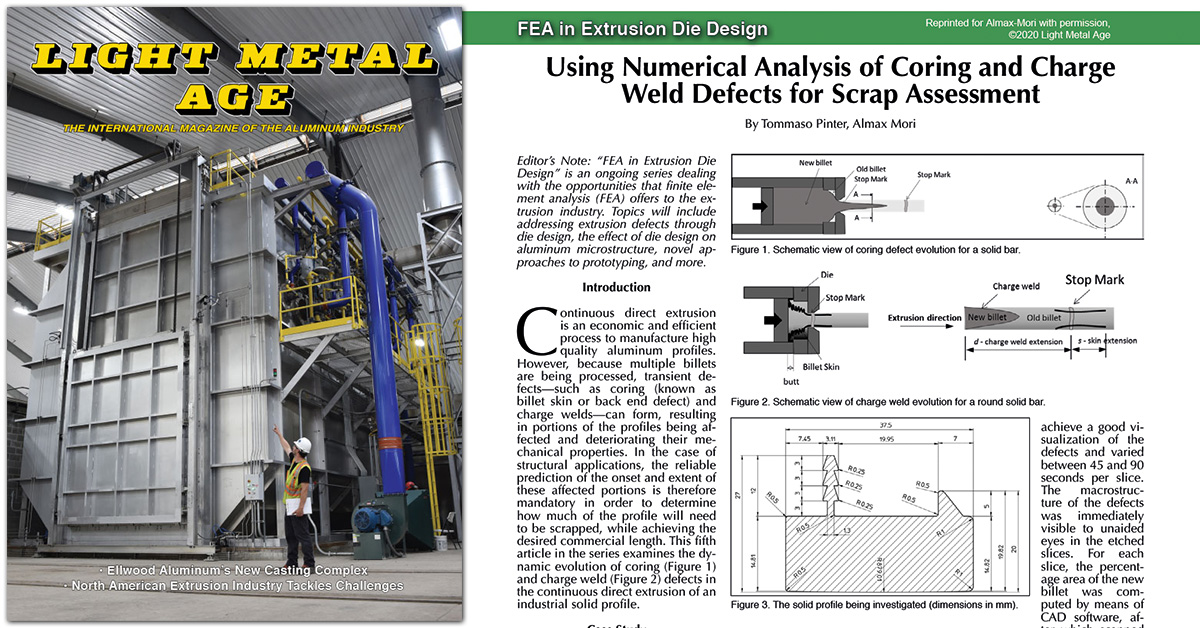
Using Numerical Analysis of Coring and Charge Weld Defects for Scrap Assessment
Abstract
Continuous direct extrusion is an economic and efficient process to manufacture high quality aluminum profiles. However, because multiple billets are being processed, transient defects - such as coring (known as billet skin or back end defect) and charge welds - can form, resulting in portions of the profiles being affected and deteriorating their mechanical properties. In the case of structural applications, the reliable prediction of the onset and extent of these affected portions is therefore mandatory in order to determine how much of the profile will need to be scrapped, while achieving the desired commercial length. This fifth article in the series examines the dynamic evolution of coring and charge weld defects in the continuous direct extrusion of an industrial solid profile.